Scaffolding
Blog
Get the latest industry news, insights and best practices.
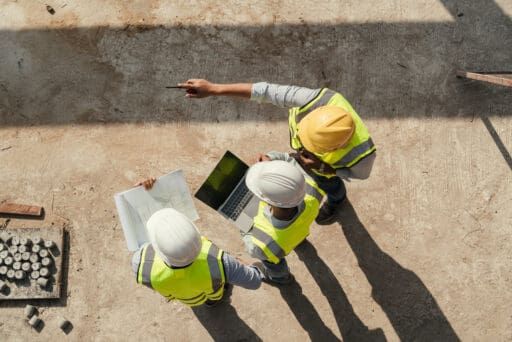
How to Improve Your Bid-to-Win Ratio & Win More Scaffolding Projects
Introduction Every scaffolding company knows the pressure of submitting bids (tenders) under looming deadlines, narrow profit margins, and high competition.… Read More
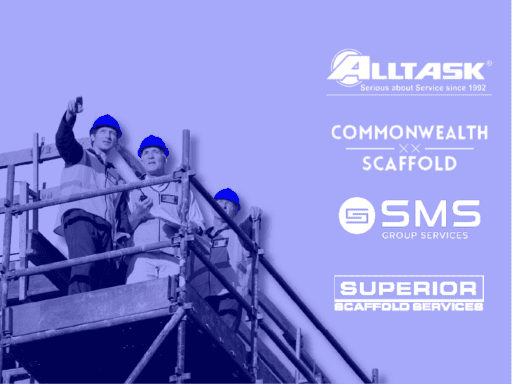
Eliminating Billing Errors & Inventory Chaos: How 4 Companies Streamlined Operations with Avontus Quantify
Managing scaffolding projects requires precision and efficiency. Yet, many companies still rely on outdated manual processes such as spreadsheets, which… Read More
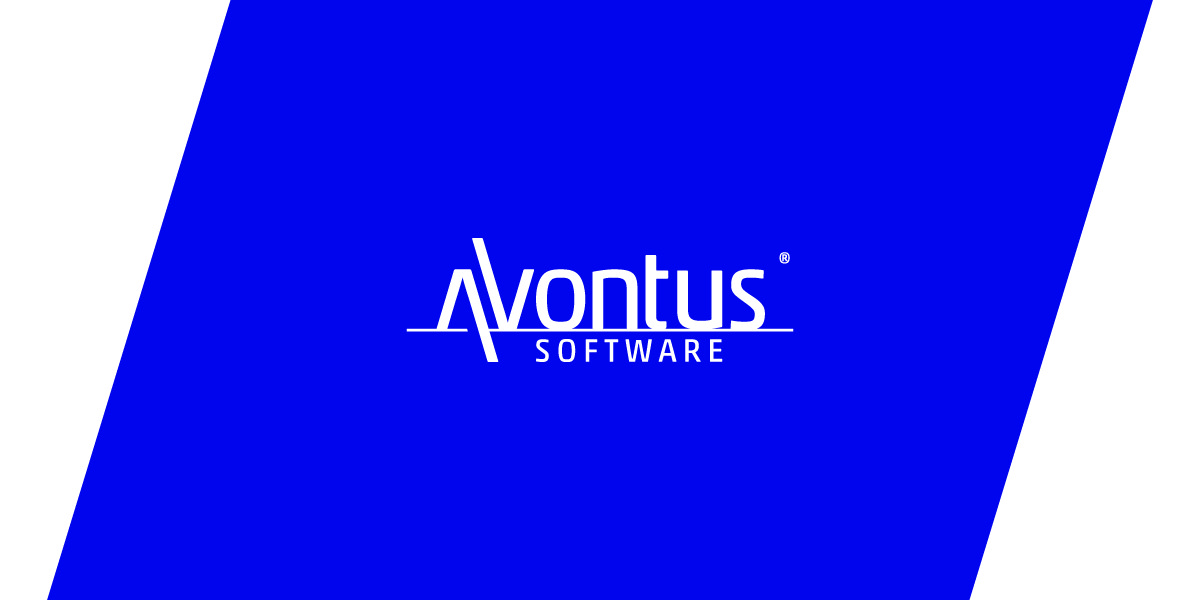
Quantify 2024 Release
Quantify 2024 is here and it comes with some great benefits: Quantify is available as a full-featured cloud solution. Our… Read More
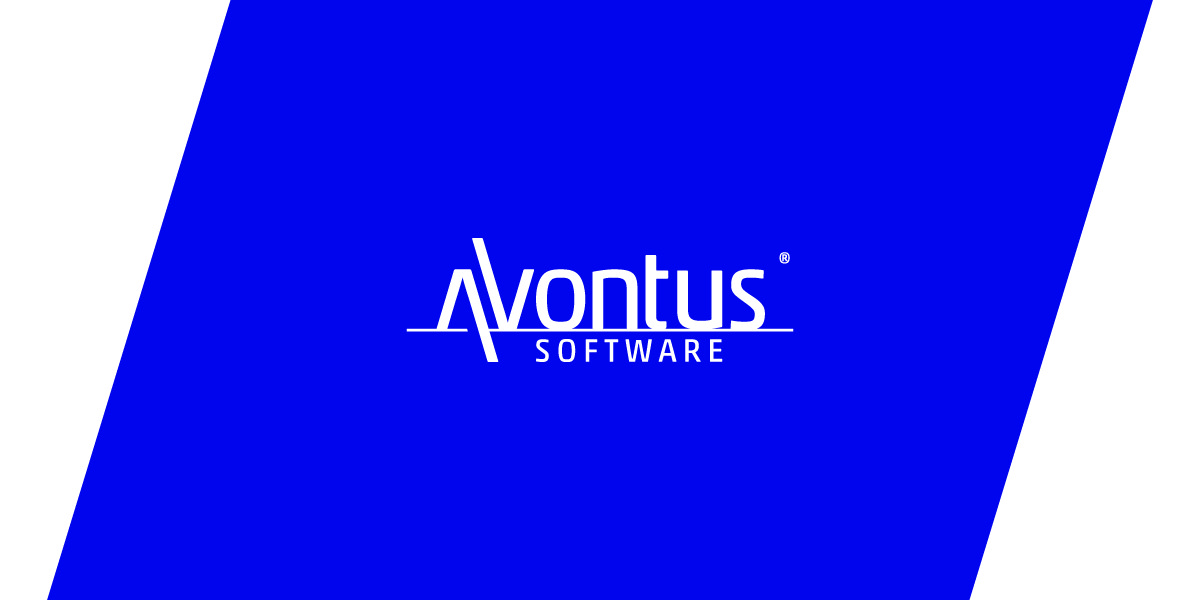
4 Reasons You Need Integrated Scaffolding Solutions
In complex cross-department collaboration, it’s crucial to ensure information accuracy and transparency throughout your projects. Maintaining visibility and communication among… Read More
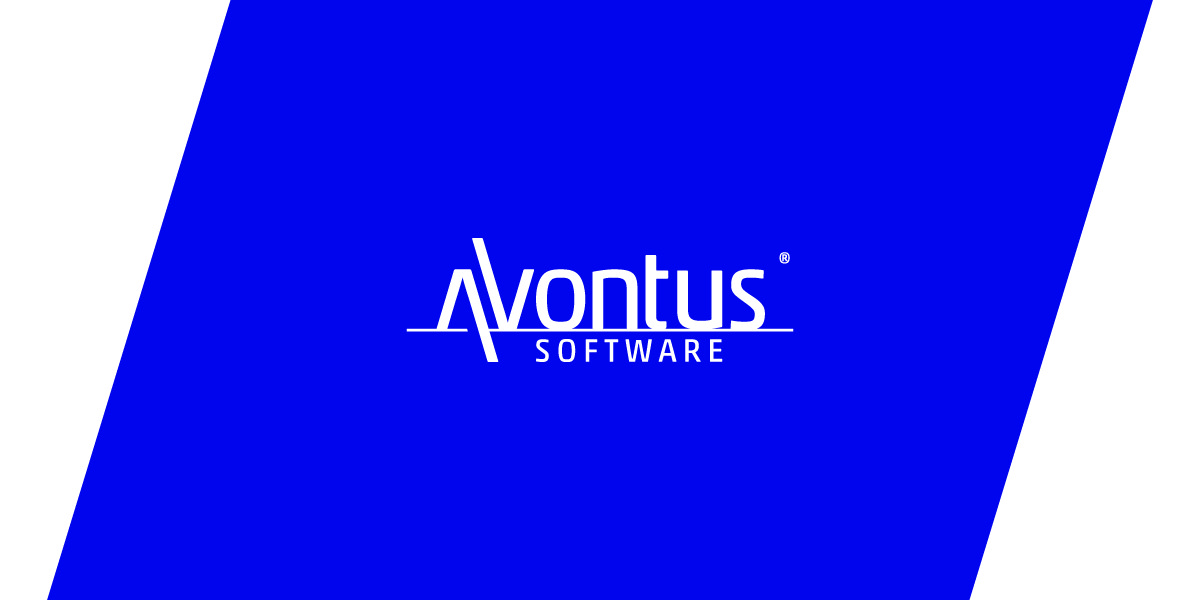
The Benefits of Scaffolding Technology Implementation in Businesses
The benefits of technology for businesses are obvious: greater efficiency, improved accuracy, and improved communication, just to name a few.… Read More